Hydrogen Fuel Cells Could Provide Emission Free Backup Power at Datacenters, Microsoft Says
By John Roach
Latham, New York – Hydrogen fuel cells packed into a pair of 40-foot-long shipping containers here ramped up on an overcast day early this June as engineers gathered around laptops displaying data on the state, health and power output of the cells in this first-of-a-kind hydrogen generator.
“This is it, it’s running at three megawatts right now,” exclaimed Mark Monroe, a principal infrastructure engineer on Microsoft’s team for datacenter advanced development.
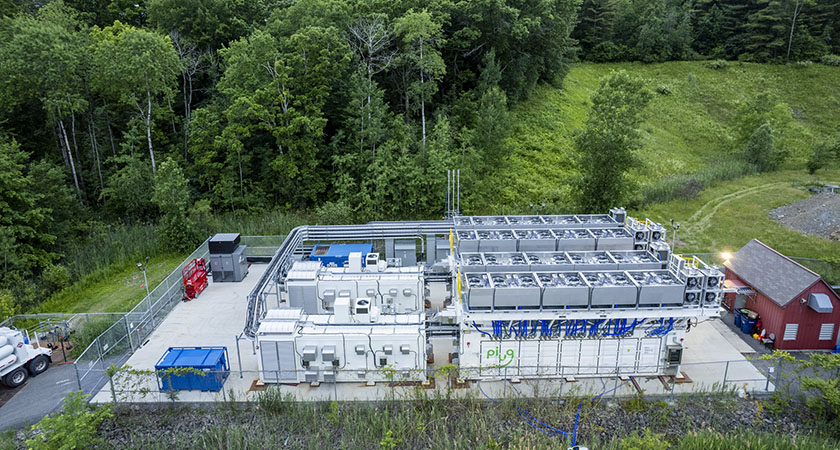
A round of applause and shouts of joy from engineers at Plug, who built the fuel cell system, pierced the white noise from fans atop the shipping containers and pipes venting steam. The moment was the latest milestone on Microsoft’s quest to find a zero-carbon emissions replacement for the backup diesel-powered generators that support continuous operations in the event of power outages and other service disruptions.
“What we just witnessed was, for the datacenter industry, a moon landing moment,” said Sean James, Microsoft’s director of datacenter research. “We have a generator that produces no emissions. It’s mind-blowing.”
Datacenters are the physical infrastructure behind the veil of cloud computing. They are where cat videos and vacation photos are stored, where remote workers gather for virtual meetings and gamers converge to build worlds, race cars and blast away foes. They enable the digital transformation of businesses around the world, allowing them to quickly and securely respond to customers’ needs and manage supply chain logistics.
At the core, datacenters are intentionally nondescript warehouses packed with tens of thousands of computer servers and the equipment needed to keep the servers running and available 24 hours a day, 7 days a week. This includes machines that keep the servers at t-shirt weather temperatures, as well as batteries and generators that maintain an uninterrupted power supply even during power grid outages.
“What makes a datacenter a datacenter is that it can operate even though the grid is not,” James said. “When there’s a blackout, the servers stay up. That’s the difference between a datacenter and a warehouse chock full of computers.”
Next-generation generator
Microsoft strives to provide datacenter customers “five-nines” of service availability, which means that the datacenter is operational 99.999% of the time. To do that, datacenter operators rely in part on the batteries in what’s called the uninterruptible power supply, or UPS, to kick on the moment a power outage occurs and provide power to the servers while backup generators are fired up.
To make sure the generators are ready at a moment’s notice, Microsoft tests them periodically, and performs what are called load tests to make sure the electrical load from the servers and other datacenter equipment can be reliably transferred to the generators.
While the backup generators are used infrequently, they are critical if there is a power outage. That’s because they maintain uninterrupted power to the datacenter, and thus service to customers.
When the backup generators do run, they typically burn fossil fuel, though Microsoft has been pioneering sustainable fuel alternatives. Microsoft has committed to eliminate diesel fuel as part of the company’s pledge to be carbon negative by 2030. To meet this goal, Microsoft is exploring short-and long-term alternatives.
For example, in November 2021, Microsoft launched its sustainable datacenter region in Sweden that uses Swedish fuel provider Preem’s Evolution Diesel Plus for generator fuel. This diesel contains at least 50% renewable raw material and nearly an equivalent reduction in net carbon dioxide emissions compared with standard fossil diesel blends.
Long term, proton exchange membrane, or PEM, fuel cell technology could be a viable solution for no carbon emissions, according to Lucas Joppa, Microsoft’s chief environmental officer. PEM fuel cells combine hydrogen and oxygen in a chemical reaction that generates electricity, heat and water – no combustion, no particulate matter and no carbon emissions.
The PEM fuel cell test in Latham demonstrated the viability of this technology at three megawatts, the first time at the scale of a backup generator at a datacenter. Once green hydrogen is available and economically viable, this type of stationary backup power could be implemented across industries, from datacenters to commercial buildings and hospitals.
“Three megawatts is super interesting because that’s the size of the diesel generators that we use right now,” Joppa said.
‘We built a vision’
Microsoft started to explore fuel cell technology in 2013 with the National Fuel Cell Research Center at the University of California, Irvine, where they tested the idea of powering racks of computer servers with solid oxide fuel cells, or SOFCs, which are fueled by natural gas. The technology shows promise for baseload power, though it is currently prohibitively expensive.
Microsoft turned to PEM fuel cells as a potential solution to the backup diesel generator challenge in 2018. PEM fuel cells are commonly used in the automotive industry because, like diesel engines, they are quick to turn on and off, and can follow a load up and down. That fast reaction and load following capability is well suited for backup power at datacenters, Monroe noted.
“We started looking at the projections of the costs and the availability of hydrogen and we started to really believe that this might be a solution. And, so, we built a vision. It took us from a rack to a row to a room to a datacenter,” he said.
In 2018, Microsoft collaborated with engineers at the National Renewable Energy Laboratory in Golden, Colorado, to power a rack of computers with a 65-kilowatt PEM fuel cell generator. Then, in 2020, the team hired Power Innovations in Salt Lake City, Utah, to build and test a system that could power 10 racks – a row – of datacenter servers for 48 consecutive hours with a 250-kilowatt hydrogen fuel cell system.
After that successful proof-of-concept demonstration, the team set out to prove the viability of a three-megawatt system, which is of sufficient size to replace a diesel generator at a datacenter.
The problem, Monroe noted, was that nobody made PEM fuel cell systems that large – three megawatts is more than 10 times bigger than the system the company tested in Utah. Three megawatts is enough energy to power about 10,000 computer servers or 600 homes.
‘The coolest thing’
The challenge to build a three-megawatt fuel cell system resonated with engineers at Latham-based Plug, a pioneer in the commercial development of fuel cell and green hydrogen technologies. Today, the company offers solutions throughout the green hydrogen ecosystem — from production and transportation to storage, handling and dispensing.
“Drawing it on the whiteboard and saying, ‘Okay, we know we can do this, we know we can do this,’ was a lot of fun,” said Scott Spink, the director of engineering for Plug. “The real challenge for this project was that we didn’t get to rely on one proven technology. Every piece of that fuel cell system came through a team that was at the forefront of what they were doing.”
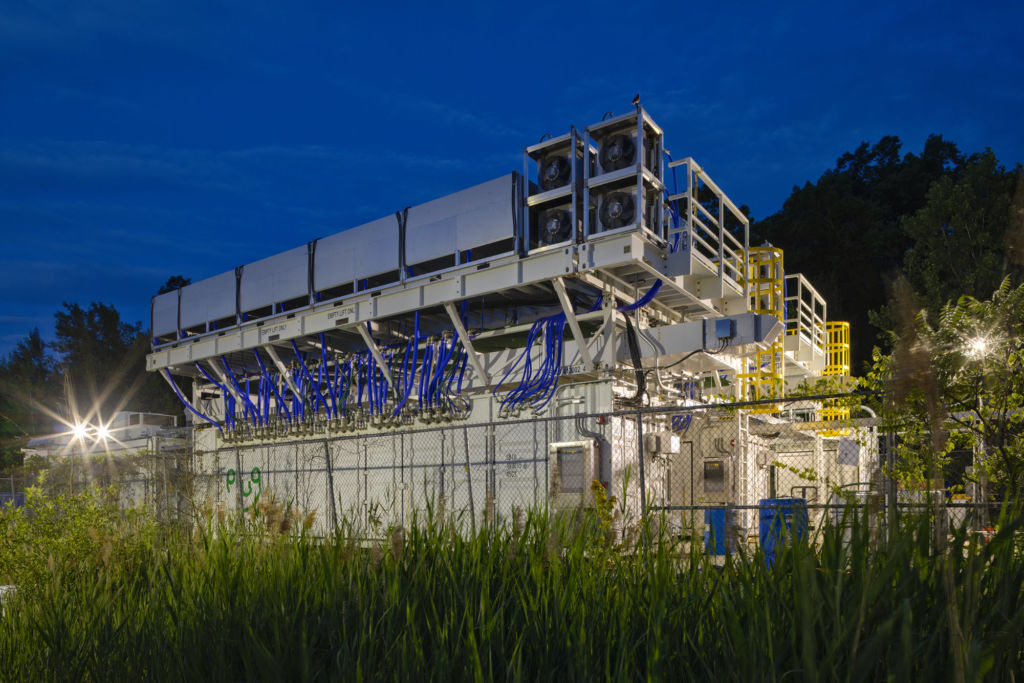
The 125-kilowatt fuel cells – 18 of which are packed into each shipping container – are the largest the company has ever made, and the three-megawatt fuel cell system is Plug’s biggest application. Because the system is larger than anything built before, so too are all the components, from compressors and heat exchangers to grid-scale inverters and the pipes for hydrogen delivery.
The system was assembled piecemeal on a concrete pad adjacent to a parking lot behind the company’s headquarters for research and development and manufacturing of its ProGen line of fuel cells. Exposed wires and tubes go this way and that and the hat of radiator fans overhangs the containers giving the system the appearance of a first-iteration prototype.
The engineers that Spink assembled to build the system were unfazed by the motley appearance.
“This is the coolest thing I’ve ever done,” said Hannah Baldwin, a next-generation electrical engineer for the high-power stationary group at Plug, who was hired to work on the project. “I don’t know how I’m going to top this in my career. There’re just so many pieces of the puzzle that have to come together. And seeing them all coming together and working well and stable is rewarding.”
Backup power
After the fuel cell generator hit the three-megawatt milestone, Microsoft’s James jumpstarted the testing to prove it could perform in real-world conditions.
“I’ve asked two questions,” he said. “My first one’s been answered: Can this technology all integrated together produce the power that I need? My second question is can it perform like a diesel? A diesel engine can produce a lot of power very quickly. That’s the key. So, we’re going to start simulating a datacenter duty cycle and one of those is a power outage.”
When a power outage occurs, batteries in the UPS can keep the datacenter running for several minutes, which is more than sufficient to ramp up a diesel – or hydrogen – generator. Once ramped up, backup generators, in theory, can keep the datacenter running indefinitely, as long as they have a fuel supply.
Starting that June day in Latham and for the next several weeks, Spink’s team ran the three-megawatt hydrogen fuel cell system through the tests Microsoft uses to qualify diesel generators to prove it could function reliably, including simulated power outages and hours-long runs.
“I’m just tickled,” Monroe said. “This is a continuation of the journey that we started back in 2018. And in 2020, when we announced the work that were doing on the smaller tests, we alluded to the fact that we were going to run a three-megawatt test sometime in the future. The future is now.”
With the prototype testing complete and concept proven, Plug is focused on rolling out an optimized commercial version of high-power stationary fuel cell systems that have a smaller footprint and a more streamlined and polished aesthetic than the one on the pad adjacent to the parking lot in Latham.
Microsoft will install one of these second-generation fuel cell systems at a research datacenter where engineers will learn how to work with and deploy the new technology, including the development of hydrogen safety protocols. The date of first deployment at a live datacenter is unknown, though it will likely occur at a new datacenter in a location where air quality standards prohibit diesel generators, James noted.
“I’m going to turn around when the excitement dies down and start to ask, ‘Okay, we did one, where can I get 1,000?’” he said. “We’ve got a commitment to be completely diesel free, and that supply chain has got to be robust – we’ve got to talk about scale across the entire hydrogen industry.”
Hydrogen economy
Hydrogen is the lightest and most abundant element in the universe. It’s long been eyed on Earth for its clean energy potential. A challenge is that while stars such as the sun consist mostly of hydrogen, on Earth hydrogen only naturally occurs in compound form with other elements – think water or hydrocarbons such as natural gas and petroleum.
The high cost and technology required to separate hydrogen from these natural compounds, store it, transport it and wring power from it at scale have limited its use. Over the past decade, that calculus has begun to change, according to Darin Painter, a vice president of sales and product management for stationary power at Plug.
The change is driven by advances across the hydrogen ecosystem coupled with a growing interest in and commitment to sustainability, he said.
For example, abundant and inexpensive wind and solar energy is enabling the cost-efficient generation of so-called green hydrogen with machines called electrolyzers. These machines operate like a fuel cell in reverse – they use energy to split water molecules into hydrogen and oxygen. If the energy used to run the electrolyzer is from renewables, then the hydrogen produced is considered green.
The hydrogen used during the Latham test was a low-carbon “blue” hydrogen obtained as a byproduct in the industrial production of chlorine and sodium hydroxide. Plug is in the process of scaling up green hydrogen production at facilities throughout the US and Europe to meet the growing demand, Painter said. Microsoft plans to use only green hydrogen in production datacenters.
At the other end of the hydrogen ecosystem, technological advances have led to denser and more efficient fuel cell stacks that combine hydrogen and oxygen to generate electricity, heat and water.
“All of that has to happen before you can get to a viable solution at scale,” Painter said. “If we would have tried to build this three-megawatt system 10 or 15 years ago, I don’t think we could have.”
Monroe and his colleagues saw this change in the calculus when they ran the numbers at the start of their hydrogen fuel cell project in 2018. On a per-watt basis, Monroe said, power produced from hydrogen fuel cells is well on the way to becoming competitive with power from other sources such as diesel generators.
To accelerate breakthroughs in clean energy solutions, the US Department of Energy announced the first Energy Earthshot – Hydrogen Shot – in June 2021, with a goal to reduce the cost of clean hydrogen by 80% to US $1 for 1 kilogram within 1 decade. A kilogram of hydrogen has roughly the same energy content as a gallon of gasoline, Monroe noted.
What’s needed, he added, is a catalyst to scale up the production of green hydrogen and fuel cells, which will drive down costs and increase adoption of the technology.
Microsoft and other players in the datacenter industry are uniquely positioned to be that catalyst, according to Joppa, who in addition to his role as chief environmental officer is Microsoft’s representative on the Hydrogen Council, a global initiative of leading energy, transport and industry companies that was formed to promote hydrogen’s role in the clean energy transition.
Microsoft’s business and sustainability needs for fuel cells and green hydrogen send a demand signal into the marketplace, Joppa noted. What’s more, if Microsoft invests in hydrogen technology and the technology works, other companies will feel more confident investing in hydrogen too, he added.
“So, if we feel confident in using these to ensure continuity of our datacenter services, that’s a big measure of faith,” Joppa said.
City-scale solutions
A robust green hydrogen economy could also help cities transition to 100% renewable energy, noted James. That’s because excess energy produced by wind and solar farms can be used to run electrolyzers, in effect storing this excess energy in hydrogen. Then, when the sun is not shining and the wind is not blowing, this green hydrogen can power fuel cells without generating any carbon emissions.
“We want to power our cloud off the sun – free clean energy,” he said. “Well, practically, how do you do that? You have to get really good at storing energy, and hydrogen is a great way to do that.”
James envisions a future where datacenters are outfitted with hydrogen fuel cells, hydrogen storage tanks and electrolyzers to convert water molecules into hydrogen with excess renewable energy. During periods of high energy demand or when the sun stops shining and the wind stops blowing, Microsoft can ramp up the fuel cells, taking the datacenter load off the grid, freeing up grid power for others to use.
The challenges of bringing a version of this vision to reality is what compels the next-generation electrical engineer Baldwin to stick with a career in the hydrogen economy, a career path, she admits, that was not top of mind before she worked on the fuel cell project.
“I’m excited about the idea of working on something that can make a difference in the world, and hydrogen has a ton of potential to be a huge game changer,” she said. “When a lot of people think of renewable energy, they think of wind turbines and solar panels, and they don’t necessarily think of hydrogen. I know I didn’t. I think that will definitely change.”